Recommended :
- Tips on Succession in FREE Subscription- Subscribes to FREE Hydrocarbon Processing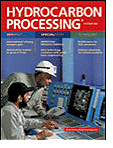
In process plant, there will be scenario for two and/or more pressure reduction devices (PRD) downstream piping discharge to a common header. Typical example is blowdown / restriction orifice to flare header. During plant wide total plant blowdown, all blowdown valves may be opened simultaneously or opened in group. Different PRD will results different level of PWL.When two Sound power sources are combined, it is understood that the total combined Sound Power Level will increase due to two energy stream are combined. However these energy streams are transmitted in wave form, the resultant Sound Power level will not be added arithmetically i.e. 1+1=2. In earlier post "
Calculate Combined Sound Power Level (PWL) Using Graphical Method", an
graphical method using PWL adder is presented.
The total combined Sound Power Level is equal to "PWL adder" (which estimated base on PWL difference between both stream and from several experience equations ) plus maximum PWL out of both streams.
Combined PWL = Maximum PWL + PWL Adder
Analytical Method This post will present another analytical method to calculate combined PWL for multiple streams (PWL1, PWL2...)
Total combined Sound Power Level
PWLC = 10 Log10 [+ 10^(PWL1 / 10) + 10^(PWL2 / 10)+...]
ExampleTwo Pressure control valves with PWL of 160 dB and 166 dB discharging to a flare header. Calculate combined PWL.
Graphical method Assumed PWL attenuation due to piping is ignored.
PWL,diff = 166 - 160 = 6 dB
PWL adder = 10 ^ (0.4771 - 0.0795 x 6) = 1 dB (
refer earlier post).
Combined PWL = Maximum PWL + PWL Adder
Combined PWL = 166 + 1 =
167 dB.
Analytical methodFrom above analytical equation,
Combined PWL = 10 Log10 [10^(166/10)+10^(160/10)]
Combined PWL = 167 dBObviously analytical method is simpler and faster.
Related Topic