Display problem ? Click HERE
Recommended :
- Tips on Succession in FREE Subscription
- Subscribe FREE - Hydrocarbon Engineering
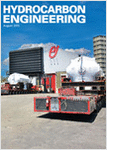
Isolation valves are provided upstream and downstream of the PSV to facilitate PSV isolation for inspection and maintenance purpose. There are several points related to this isolation valve and other recommendations in "Concerns & Recommendations on PSV INLET line" and "Few Concerns & Recommendations of PSV Discharge Tail pipe". These isolation valves are normally either Car Seal Open (CSO) or Locked Open (LO) to avoid operator inadvertently close these valves, unless required by safety analysis i.e HAZOP. Read more about Car Seal and Lock system in "How CSO and CSC helps ?" and "Locked Valve Increases Security, Reliability & Integrity".
- Tips on Succession in FREE Subscription
- Subscribe FREE - Hydrocarbon Engineering
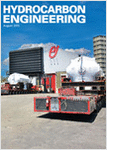
Isolation valves are provided upstream and downstream of the PSV to facilitate PSV isolation for inspection and maintenance purpose. There are several points related to this isolation valve and other recommendations in "Concerns & Recommendations on PSV INLET line" and "Few Concerns & Recommendations of PSV Discharge Tail pipe". These isolation valves are normally either Car Seal Open (CSO) or Locked Open (LO) to avoid operator inadvertently close these valves, unless required by safety analysis i.e HAZOP. Read more about Car Seal and Lock system in "How CSO and CSC helps ?" and "Locked Valve Increases Security, Reliability & Integrity".
Increases demand on plant availability and operability lead to sparing of Pressure Relief Valve (PSV). Nevertheless, there is different philosophy on the isolation valve position in the event present of spare PSV. Let see the following image.
Isolation Valve Position
- Duty PSV Inlet & Outlet
The duty PSV inlet and outlet PSV are in OPEN position to ensure 100% flow path when it is on demand.
- Spare PSV Inlet
The spare PSV inlet isolation valve should be in CLOSE position to minimize possibility and occurrence of PSV passing due to damaged and imperfect seat during normal operation and PSV chattering in case the overpressure scenario occurred.
- Spare PSV Outlet
The spare PSV outlet isolation valve should be in OPEN position to avoid the situation where pressure built-up, condensation and corrosion of the section between spare PSV outlet and isolation valve in case of valves passing (inlet isolation and PSV passing.
How PSV chattering occur in case both Valves are in OPEN position ?
There are several factors lead to occurrence of PSV chattering.
Factor (i) Excess Relief Area
- For a system protected with 2 x PSVs with identical set pressure as shown in above images, if both PSVs inlet are in OPEN position and in the event pressure built-up to set pressure, both PSVs will pop open. 200% of opening area serving 100% relief flowrate, this would evacuate the internal contents sharply, internal pressure decreases quickly and reduce overpressure range (percentage overpressure above set point reduce). Both PSVs will quick move into PSVs reseating cycle. As flow into 2 x PSVs, half of the relief flow (assumed perfect distribution) will goes into 1 x PSV, during reseating cycle, reduced flow will cause less force on the disc and reduce blowdown (as both PSV's blowdown were set for 100% flow). The blowdown reduction could be high and cause blowdown less than 7% as normally requested by API. Reduced overpressure and blowdown would cause PSV chatter and damage PSV disc and seat.
Factor (ii) Imperfect flow distribution
Factor (i) Excess Relief Area
- For a system protected with 2 x PSVs with identical set pressure as shown in above images, if both PSVs inlet are in OPEN position and in the event pressure built-up to set pressure, both PSVs will pop open. 200% of opening area serving 100% relief flowrate, this would evacuate the internal contents sharply, internal pressure decreases quickly and reduce overpressure range (percentage overpressure above set point reduce). Both PSVs will quick move into PSVs reseating cycle. As flow into 2 x PSVs, half of the relief flow (assumed perfect distribution) will goes into 1 x PSV, during reseating cycle, reduced flow will cause less force on the disc and reduce blowdown (as both PSV's blowdown were set for 100% flow). The blowdown reduction could be high and cause blowdown less than 7% as normally requested by API. Reduced overpressure and blowdown would cause PSV chatter and damage PSV disc and seat.
Factor (ii) Imperfect flow distribution
Apart from reduce flow 100% to 50% each PSV, different inlet pipe routing, different fouling or corrosion level in the inlet piping would lead to mal-distribution of flow into each PSV. This would cause even less flow (less than 50% ) into one of the PSV. Imperfect flow distribution on the inlet line would made the overpressure and blowdown even lower and promote PSV chattering
Factor (iii) Non-equal spring force and friction
Non-equal spring force, friction , etc between both PSVs in real world operation possibly resulted 1 x PSV open slightly faster than the other. This subsequently lead to both PSV's spring seeing different pressure on disc. One PSV might be on opening cycle and the other on closing cycle. The PSV on opening cycle will experience less force and tends to close while the PSV on closing cycle will experience more force and tends to open more. Until a point, both PSVs opening - closing cycle will exchange. Both PSV will fighting each and other. This is another type of PSV chattering phenomenon. Again, mal-distribution of flow would promote this phenomenon.
PSV Chattering
PSV Chatter is rapid reciprocating motion of the disc where the disc contacts with the seat in cyclic motion. Chatter is destructive where it repetitive and rapid reciprocating disc knock on the valve seat may cause
i) damage to the disc & valve seat lead to leakage and passing
ii) damage to bellow lead to gas leak via bonnet vent
iii) damage to the PRV itself and interconnecting piping through vibration
iv) severe noise level
Read more in "PSV Chaterring is Destructive...The ways to Prevent..."
Besides above discussion, read may also encourage refer to API RP 520 part 2 (2000 rev), section 6.3.3 recommendation.
Related Posts
PSV Chattering
PSV Chatter is rapid reciprocating motion of the disc where the disc contacts with the seat in cyclic motion. Chatter is destructive where it repetitive and rapid reciprocating disc knock on the valve seat may cause
i) damage to the disc & valve seat lead to leakage and passing
ii) damage to bellow lead to gas leak via bonnet vent
iii) damage to the PRV itself and interconnecting piping through vibration
iv) severe noise level
Read more in "PSV Chaterring is Destructive...The ways to Prevent..."
Besides above discussion, read may also encourage refer to API RP 520 part 2 (2000 rev), section 6.3.3 recommendation.
Related Posts
- Concerns & Recommendations on PSV INLET line
- Concerns & Recommendations of PSV Discharge Tail pipe
- How CSO and CSC helps ?
- Locked Valve Increases Security, Reliability & Integrity
- Relate PSV Relieving Flow to Stamped Capacity
- Thermal Relief of Non-Flashing Liquid in Pipe
- Simple Flow Chart to Determine Requirement of Thermal Relief
No comments:
Post a Comment