Display problem ? Click HERE
Recommended :
Subscribe FREE - Processing Magazine
Depressuring system is commonly provided in Oil and gas facilities to facilitate system inventory blowdown to a safe level within a reasonable time during emergency situation. Detail requirements may refer to API Std 521 section 5.20.1. Conventionally depressuring system consist of Blowdown Valve (BDV) with Restriction Orifice (RO) located some distance (about 600mm) downstream of BDV. Read "Why Restriction Orifice is some distance from Blowdown valve ?" to understand more the distance requirement. Beside, there are controlled and non-controlled Type Depressuring. Second type of non-controlled depressuring is a throttling device with control function into it.
Subscribe FREE - Processing Magazine
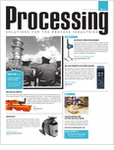
Recently some smart engineers have proposed to use the second type with throttling device to replace the conventional BDV (ball valve) plus RO type based on following reasons :
- Ball valve opens too quickly which may cause bending of RO leading to size changes and higher flow on next use.
- Ball valve does not throttle flow and opening will erode the ball & sealing. Globe valve, with soft seats, will have minimal damage and can also be used for pressure control.
- Globe valve with control function will increase the blowdown rate with gradual opening in later stage
Minimium (almost none) reported case in the failure of RO
High flow leading to bending of RO and subsequently cause higher flow and low temperature issue of blowdown vessel might be one of the credible concern in conventional BDV plus RO system. Beside, erosion & cavitation occured at the RO possibily lead to larger RO. Althought this concern is valid, however there are minimium (almost none) reported case in the failure of RO in this regard. The could be credited to a infrequent use, proper blowdown rate determinination, correct material selection, properly calcuated RO bore size.
Excessive Flow When Control Function FailureHigh flow leading to bending of RO and subsequently cause higher flow and low temperature issue of blowdown vessel might be one of the credible concern in conventional BDV plus RO system. Beside, erosion & cavitation occured at the RO possibily lead to larger RO. Althought this concern is valid, however there are minimium (almost none) reported case in the failure of RO in this regard. The could be credited to a infrequent use, proper blowdown rate determinination, correct material selection, properly calcuated RO bore size.
Conventionally a valve with control function will be sized to open at 75-85%. With the characteristic of valve i.e. equal percentage and remaining 15-25% opening would results a flow of 2-3 time when it is FULLY OPEN. Employing a globe valve with control function, whenever the control function is failed and derive a maximum signal to open the glove valve fully, it will results excessive flow to the downstream disposal system. Large and costly disposal system is expected.
Difficult Valve Characteristic Selection
If a quick opening valve is selected to reduce the large flow during valve full open , this will partially cause inefficient control during low flow. Additional effort is required on valve characteristic selection.
Reliability, Availability & Cost Effective
Reliability and Availability of blowdown with control valve is another concern. Conventional BDV (ball valve) is spring to open, double solenoid valves, volume bottle, high SIL Blowdown system lead to increase safety integrity. Use of control valve may experience difficultites in meeting the safety integrity or high cost is incurred. Thus, a proper relaibility, availability and cost effective solution may have to considered.
Concluding remark
Above proposal certainly a good idea to be investigated in detail as there is a great potential in assisting system blowdown in shorter time and reduce overall safety risk. A proper discussion shall be included to address the issue as highlighted above in order to provide a cost effective but not tolerating any safety concerns.
Related Post
- Few Recommendation on Manual Blowdown Line
- A refresh to Process Engineer on few phenomenons in restriction orifice
- Bug in ASPENTECH HYSYS 2006 Dynamic Depressuring Fisher Valve model
- Controlled and Non-controlled Type Depressuring
- How to apply valve equation in HYSYS Depressuring ?
- Why Restriction Orifice is some distance from Blowdown valve ?
- Restrcition Orifice Used in Many Applications in Different Manners
No comments:
Post a Comment