Display problem ? Click HERE
Recommended :

Steam is commonly used in oil & gas, refinery, petrochemical and power plant for heating and power generation. Steam is condensed in equipment for heating and in turbine for power generation. Condensate is then collected in common collector before it is sent to condensate drum. Condensate from drum is then pumped to Boiler for steam generation via a Boiler Feed Water (BFW) pump. BFW is normally a centrifugal type and a minimum flow recirculation line is provided on BFW discharge for pump protection.
Minimum flow control can be
- a flow meter on pump discharge with control valve on recycle line
- a flow-Delta P and flow meter on pump discharge with control valve on recycle
- an automatic Recirculation Valves (ARC) valve
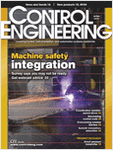
There are several problems assocaited with these valves in condensate recycle line :
i) Erosion - flashing and cavitation results trim and body erosion
ii) Severe noise and vibration - flashing and cavitation
iii) Leakage - energy loss
Recommendation
Several recommendations to miniminse above mentioned problems :
i) Harden trim to resist erosion cause by flashing and cavitation
ii) Correct material i.e. alloy selection to avoid erosion-corrosion
iii) Anti-cavitation trim to minimise / avoidance of cavitation.
iv) Multi-stage anti-cavitation trim for small valve
v) Multi-hole anti-cavitation trim for large valve
vi) Multi cage anti-cavitation trim for high pressure recovery (FL) valve
vii) High lift (more than 20% lift) valve to increase trim life
viii) Large body valve to minimise velocity (high velocity lead to high erosion) in the valve inlet and outlet chambers. [Tips : Body erosion proportional to 3-5 power of velocity]
ix) Elevate condensate drum to increase back pressure to the valve (if possible)
x) Provide restriction orifice downstream of control valve to increase back pressure. One shall take note at low flow, the pressure drop acrosss RO is negligible. Majority pressure drop (energy being "killed") still occurred at valve
xi) Tight shut off (class V) valve to avoid leakage and hence energy loss.
Related Topic
No comments:
Post a Comment