Display problem ? Click HERE
Recommended :
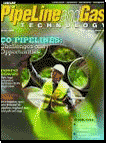
(i) Vapor & Liquid Recover to Source
In a plant, there may consist several production trains with common flare system. This is one of the strategy to minimize capital investment cost. Typical plant with multiple trains and common flare is Liquefied Natural Gas (LNG) and gas processing plant. Example Qatar gas LNG plant has at least 7 trains, Australia North West Shelf has at least 5 trains, etc. Although all trains are located in same place sharing common flare system, however the owner of these train may be different. Probably Train 1, 2 & 3 are owned by company ABC, train 4 & 5 own by company MMM and train 6 & 7 own by company XYZ. Vapor and liquid hydrocarbon leaks or relief from a train, this valuable hydrocarbon may be recovered back to its train process system by same owner. Thus, providing a dedicated KOD for trains belonging to dedicated owner may serve above purpose.
(ii) Design limitation of Main Flare On Operational Non-Smoking Requirement
Common main flare shall be designed for largest load from all trains in any relieving scenario. Common relieve scenario contributes to large relief load are cooling water failure, total power failure, total plant blowdown, etc. This possibly lead to common main flare with large capacity. However, it is also common requirement to have non-smoking flaring during normal operation with low flow. As common main flare with large capacity may have limited turndown and exceeded the minimum normal operational flow, thus a dedicated operational flare may be provided for train(s) with same owner. Providing a dedicated KOD and operational flare for trains belonging to dedicated owner may serve above purpose.
iii) Mixing of Product may not be recoverable in any plant
Some plants with common flare system but relieve different of product. There is potential the mixture of the products may not be recoverable by any of the plant. Thus, a dedicated KOD for dedicated plants are provided so that the product relief from dedicated plant is recoverable in the plant which relieved the fluid.
(iv) Mixing of Fluid Cause Slugging
Common main flare system for plant with hot fluid and cold fluid may lead to condensation and results slugging flow in the flare header. Slugging in flare header potentially results severe erosion, noise and vibration. Providing a dedicated KOD will remove liquid from the relieve fluids and minimise the potential of slugging in the common header. This may only minimise, but not totally avoid as hot vapor may still mix with cold vapor in the common header and condensation/slugging flow may still possibly present. However, providing of dedicated KOD will reduce the slugging flow potential. In the event, severe slugging still possibly present and results problem to flare support, it is always advisable to provide separate flare system.
(v) Reduce Common Header Size
Providing dedicated KOD would possibly reduce relief flow (liquid) to the common header during common relief scenario. Reduction in relief flow will reduce the main flare header size.
Related Topic
No comments:
Post a Comment