Display problem ? Click HERE
Recommended :
Subscribe FREE - Pipeline Oil & Gas Journal
Vapor stream from column top is normal condensed via a partial or total condenser before it feed into a reflux drum. When the simulation is done in HYSYS environment with standard column template (with condenser), HYSYS only calculate the heat removal in term of energy. However, as the condenser is water cooled, how shall we estimate the water flowrate ?
Subscribe FREE - Pipeline Oil & Gas Journal
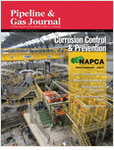
Above was a question raised by a young engineer, it is a basic fundamental question. It could be simple to many of you who familiar with stream transfer and working with sub-flowsheet environment.
Let take an example. A condensate stabilizer with overhead condenser and condensate reboiler simulated in HYSYS as shown in following image.
Overhead vapor will be cooled by cooling water feeding from plant cooling water system while the reboiler is heated by plant hot oil system. The main simulation is using standard Equation of State (EOS) of Peng-Robinson (PR). To accurately estimate quantity of cooling water, the expected thermodynamic model is ASME steam.
If you have not known, only one Thermodynamic model (either PR or ASME Steam) can be used in single flowsheet. However, present demand is to use two thermodynamic models simultaneously.The way to handle above situation is to create a new flowsheet working in ASME Steam model while maintaining PR model in main flowsheet.
Include new sub-flowsheet
Include a Standard Sub-Flowsheet using Add Operation in Flowsheet pull down menu. Attach the energy stream Q-100 in to the sub-flowsheet FLOW-1 as shown in following image.
Define ASME Steam thermodynamic model
Enter Basis Environment sheet to define ASME Steam thermodynamic model as Basis-2. The default Basis-1 should have been assigned to PR EOS. Ensure Fluid-package-to-use for FLOW-1 sub-flowsheet is assigned to Basis-2.
Simulate Cooling Water Loop in Sub-Flowsheet FLOW-1
Enter into Sub-Flowsheet FLOW-1. The water cooler can be simulated as shown in following image.
Conclusion remark
Using Stream Transfer and Sub-Flowsheet capability, you can simulate all process and utilities systems simultaneously. This is a way to minimize transfer error, instant value update, understand how process system impacting utilities system, etc. However, it will generate a very large simulation file which will potentially required a very sophisticated computer hardware to speed-up the processing works.
Related Topic
Let take an example. A condensate stabilizer with overhead condenser and condensate reboiler simulated in HYSYS as shown in following image.
Overhead vapor will be cooled by cooling water feeding from plant cooling water system while the reboiler is heated by plant hot oil system. The main simulation is using standard Equation of State (EOS) of Peng-Robinson (PR). To accurately estimate quantity of cooling water, the expected thermodynamic model is ASME steam.
If you have not known, only one Thermodynamic model (either PR or ASME Steam) can be used in single flowsheet. However, present demand is to use two thermodynamic models simultaneously.The way to handle above situation is to create a new flowsheet working in ASME Steam model while maintaining PR model in main flowsheet.
Include new sub-flowsheet
Include a Standard Sub-Flowsheet using Add Operation in Flowsheet pull down menu. Attach the energy stream Q-100 in to the sub-flowsheet FLOW-1 as shown in following image.
Define ASME Steam thermodynamic model
Enter Basis Environment sheet to define ASME Steam thermodynamic model as Basis-2. The default Basis-1 should have been assigned to PR EOS. Ensure Fluid-package-to-use for FLOW-1 sub-flowsheet is assigned to Basis-2.
Simulate Cooling Water Loop in Sub-Flowsheet FLOW-1
Enter into Sub-Flowsheet FLOW-1. The water cooler can be simulated as shown in following image.
Conclusion remark
Using Stream Transfer and Sub-Flowsheet capability, you can simulate all process and utilities systems simultaneously. This is a way to minimize transfer error, instant value update, understand how process system impacting utilities system, etc. However, it will generate a very large simulation file which will potentially required a very sophisticated computer hardware to speed-up the processing works.
Related Topic
- Some Tips on Glycol Regeneration Process Simulation
- Open HYSYS File in Older Version of HYSYS
- Transfer ALL Streams or Unit Operations Properties From Hysys File to Another Hysys File
- Transfer SINGLE Stream or Unit Operation Properties From Hysys File to Another Hysys File
- A Great Material In Traininig Young Engineer in HYSYS
- Useful Documentation for HYSYS ...
- Properly Simulate a Separator with Demister in HYSYS
No comments:
Post a Comment