Display problem ? Click HERE
Recommended :
Subscribe FREE - Processing Magazine
Liquid (operating temperature lower than maximum solar heating temperature) trapped in pressure vessel and piping and expose to solar heating, heat transfer into the liquid would cause liquid expansion. As liquid is “incompressible”, pressure can built up quickly and reach the maximum allowable working pressure (MAWP) of equipment and piping.
Subscribe FREE - Processing Magazine
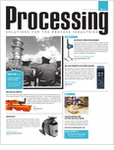
Pressure Vessel
For pressure vessel, the design code i.e. ASME Section 8 Div II always request a Pressure Relief Valve (PSV) for fire protection, thus this PSV would serve the thermal relief as well.
Piping
There is no such requirement for piping in general. However, API STD 521 2007 Addendum May 2008, section 5.14.1 (c) stated that hydraulic expansion due to solar heating on piping shall be assessed and checked if a pressure relief valve (PSV) is required. This section allows that a PSV may not required for thermal relief if proper administrative procedures and addition of signs stipulating the proper venting and draining procedures when shut-down and block-in are implemented. These action are acceptable and considered do not compromise the safety of personnel or equipment.
Common case
System under consideration for thermal relief consists of piping only (does not contain pressure vessels or heat exchangers), a pressure-relief device might not be required to protect piping from thermal expansion if :
- the piping is always contains a pocket of non-condensing vapour, such that it can never become liquid-full (even it is heated and compressed); OR
- the piping is in continuous use (i.e., not batch or semi-continuous use) and drained after being blocked-in using well supervised procedures or permits; OR
- the fluid temperature is greater than the maximum temperature expected from solar heating (the pipe temperature direct under solar heating can reached approximately 60 °C to 70 °C, it can be as high as 85 °C for certain area i.e. Middle east) and there are no other heat sources such as heat tracing; OR
- the estimated pressure rise from thermal expansion is within the design limits of the equipment or piping.
Some engineer may considered that insulates and buries pipe would avoid thermal relief. This is still an arguable statement. Insulation and buries would reduce heat inputs into the system, however, it does not completely avoid thermal relief. For example. an Liquefied Natural Gas (LNG) line from LNG plant to LNG storage may travel some distance. Although the line is insulated, the operating temperature of this can be as low as -140 degC to -150 degC. As compare to ambient temperature, there is still potential of heat leakage via insulated line and results vaporization.
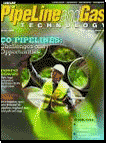
Special case
For some special case, a long piping i.e. piping between unit and/or plant may potentially experience overpressure caused by solar heating. A small Pressure Relief Valve is general provided for overpressure protection due solar heating.
The length and diameter of the piping and PSV with D-orifice sufficiently prevent overpressure protection are still remain a question.
The following studies will try to figure out the length and diameter limit for a D-orifice PSV.
Methodology
Method stipulated in API STD 521 2007 Addendum May 2008 section 5.14.3 will be used to calculate the pressure rise and liquid expansion rate (hence thermal relief rate).
Pressure rise is estimated with following equation
Where
Where
Isothermal compressibility coefficient is estimated base on :
Where
Liquid expansion rate is estimated base on :
Where
Assumption & Basis
Several assumption & basis have been considered :
- Solar heating is potentially ranging from 0.79 to 1.04 kW/m2. Nevertheless, 1.15 kW/m2 has been considered in this study for conservativeness.
- As it is difficult to ensure if total or partial piping surface area of the pipe is expose to solar heating, thus entire (100%) surface area of the pipe is assumed expose to solar heating.
- It is assumed solar heating potential heat the piping and liquid to 60°C.
- Design pressure of the piping is at 16 barg. It is considered the PSV will open at 16 barg.
- It is considered that the fluid content and piping has been heated and pressure has built-up to 15.9 barg (0.1 bar below the PSV set pressure). This will potentially lead to maximum liquid relieving rate.
- The studies have considered water(H2O), I-butane (iC4), hexane (C6), nonane (C9) and decane (C10)
- For 150# Carbon Steel (CS),
- Linear expansion coefficient is taken as 1.21 x 10-5 1/°C
- Modulus of Elasticity is taken as 207 x 106 kPa
- Wall thickness is taken as 6.35mm
Refer to following figure.
For a pipe with ID of 1524mm, the maximum pipe length lead to flow limit of D-orifice are listed as follow :
Water - 3026 m
C10 - 1365 m
C9 - 1311 m
C6 - 1029m
iC4 - 556m
If a pipeline contain iC4 with length less than 556m, a D-orifice is sufficient to protect the pipeline from solar heating overpressure protection. If exceeded 556m, a E-orifice or 2 x D-orifice may be required.
Refer to following figureFor a pipe containing iC4 (and C6 for second case), the maximum length for different pipe diameter are listed as follow :
ID - iC4 - C6
ID = 150mm - 5910 m - 11684 m
ID = 250mm - 3534 m - 6943 m
ID = 500mm - 1751 m - 3393 m
ID = 750mm - 1158 m - 2214 m
ID = 1000mm - 861 m - 1628 m
ID = 1250mm - 683 m - 1279 m
ID = 1524mm - 556 m - 1029 m
ID = 150mm - 5910 m - 11684 m
ID = 250mm - 3534 m - 6943 m
ID = 500mm - 1751 m - 3393 m
ID = 750mm - 1158 m - 2214 m
ID = 1000mm - 861 m - 1628 m
ID = 1250mm - 683 m - 1279 m
ID = 1524mm - 556 m - 1029 m
Any point below under curve implies a D-orifice is sufficient.
Concluding remark
Above briefly inform that only a small PSV (i.e D-orifice) is required for thermal relief for piping. Length limitation has been quickly established.
Related Post
- Back Pressure Affect Conventional PSV Set Pressure : Case Study #2 - Non-Bonnect Vent
- Back Pressure Affect Conventional PSV Set Pressure : Case Study #1 - Bonnect Vent to ATM
- How Back Pressure Affect Conventional PSV Set Pressure Subject to It Vent
- Several Impact of Backpressure on Conventional PSV
- Simple Flow Chart to Determine Requirement of Thermal Relief
- Why Rupture (RD) Upstream of Pressure Relief Valve (PRV) ?
- Why Two Rupture Discs in Series ?
- Tube Rupture : Pressure Relief Valve (PSV) or Rupture Disk (RD) ?
- Criteria for Requirement of Pressure Relief Device for Tube Rupture
No comments:
Post a Comment