Display problem ? Click HERE
Recommended :
- Subscribe FREE - Chemical Engineering
- Tips on Succession in FREE Subscription
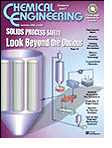
Several concerns & recommendations on Pressure Relief Valve (PSV) discharge line has been discussed in "Few Concerns & Recommendations of PSV Discharge Tail pipe". Subsequent to this posting, questions has been raised on the PSV Inlet line.
What are the concerns & recommendation on the PSV inlet line ?
- Subscribe FREE - Chemical Engineering
- Tips on Succession in FREE Subscription
Several concerns & recommendations on Pressure Relief Valve (PSV) discharge line has been discussed in "Few Concerns & Recommendations of PSV Discharge Tail pipe". Subsequent to this posting, questions has been raised on the PSV Inlet line.
What are the concerns & recommendation on the PSV inlet line ?
Issue relates to PSV Inlet Line
Let see those issue relates to PSV inlet line :
- First far most important is undersized PSV inlet line results excessive inlet line frictional loss (non-recoverable line loss) and leads to PSV chattering. Repetitive and rapid reciprocating disc knock on the valve seat may damage PSV disc & valve seat, severe vibration and noise level.
- Excessive inlet line loss also lead to overpressure of protected equipment (which is exceeded the allowable by code)
- Low pocket due to inlet line routing would leads liquid accumulation. liquid accumulation would promote corrosion.
- Liquid accumulated in inlet piping due to incorrect routing. Whenever PSV is lifted, large vapor flow will put the liquid column (at very high velocity) will knock at the PSV disc and create severe surge (water hammer) and vibration to the PSV inlet line, outlet line and PSV itself. Surging and vibration may damage PSV and associated line.
- Large liquid column formed at the inlet to PSV (those elevated PSV will results overpressure of protected equipment.
- If solid present in fluid, there is potential of solid accumulated in low pocket and may lead to complete blockage of inlet line. This defeat the purpose of PSV.
- Excessive inlet line length and elbow increases line loss
- Present of devices i.e gate valve, reduced bore ball valve, butterfly valve (read more in "Should we install Butterfly valve for Pressure Relief Valve (PSV) isolation ?"), check valve, etc and/or fittings which having reduce flow path at the inlet line. Reduced flow path potentially increase line loss and causes problem associated with large inlet loss as discussed above. API RP 521 do not permit total cross sectional area (flow path) of valve or fitting less than total PSVs area.
- Isolation valve accidentally close by operator - potentially lead to overpressure of protected system
- Isolation valve at the inlet line lose may "self close" during relief or blowdown due to vibration. "Self-close" is high torque caused by asymmetric pressure distribution in the inner surface of isolation valve lead to self closure- potentially lead to overpressure of protected system. High torque may break normal duty locking plate of the valve.
- Inlet line expose to high pour point fluid, fluid may precipitate, crystallize or polymerize, etc, ambient cooling on stagnant fluid at inlet pipe may potentially precipitate/polymerize/crystallize/solidify at the inlet line (even though no low pocket) and reduce inlet line free flow path.
- Large pressure drop across PSV during relief would results fluid (downstream of PSV) temperature drop to subzero (due to JT effect). The inlet valve may possibly cooled to subzero due to heat conduction. Moisture content around inlet valve may form ice and cause the valve stuck at position.
After understand the potential issue related to inlet, there are few recommendations that may be considered for inlet line :
- Increases inlet line size, reduce number of elbows and fittings to minimize inlet line loss (non-recoverable loss). Ensure inlet line loss (non-recoverable loss) is maximum 3% of set pressure (as per API RP 521) except permitted by API RP 521 Part II, section 4.2.3 i.e. installation of pilot operated PSV. The inlet line loss shall be based on PSV rated flow.
- No pocket at the inlet line. A special note shall be indicated in the P&ID (generalized in legend)
- Do not installed valve, fitting or device with potential of internal failure i.e butterfly valve, check valve, etc
- Consider to install PSV with larger inlet flange to avoid high velocity of the inlet pipe (after reducer). Detail may refer to API Std 526
- Car Seal Open (CSO) or Locked Open (LO) of all manual isolation valve, unless required by safety analysis i.e HAZOP
- Remove handle to minimize the opportunity of operation of isolation valve and reduce potential of self closure of valve, unless required by safety analysis i.e. HAZOP
- If ball valve is installed, Full Bore (FB) ball valve to be used.
- When valve is locked by a locking plate, consider to install heavy duty locking plate to minimize potential of self-closure
- Consider to install valve with "high torque for closure" to minimize potential of self-closure
- Ensure valve vertically upward to minimize potential of self-closure
- Consider to use gate valve to minimize potential of self-closure, if it is inline with plant wide isolation philosophy
- If gate valve is used, ensure the valve stem and handle is at least 45deg incline downward to avoid blockage due failure of valve internal
- Relocate isolation valve away from PSV i.e. relocated valve to upstream of reducer may reduce the risk of self closure due high vibration.
- Ensure inlet pipe is self drained back to protected vessel or pipe to minimize potential of liquid present in inlet line
- Ensure flow path (cross sectional area) of inlet line is more than total cross sectional area of ALL PSVs area.
- For inlet line expose to high pour point fluid, fluid may precipitate, crystallize or polymerize, etc, consider to provide insulation of inlet line to minimize heat loss and precipitate / polymerize / crystallize / solidify.
- Subject to severity of ambient cooling and potential of precipitate / polymerize / crystallize / solidify, may consider heat trace the inlet line. Whenever heat trace in installed, the integrity and reliability of heat trace shall be ensured.
- For inlet line expose to high pour point fluid, fluid may precipitate, crystallize or polymerize, etc, the PSV tapping location shall be installed to minimize liquid / solid carry into the inlet line i.e. top of vessel instead of pipe. Read more in "Where to Locate the PSV Inlet Nozzle ?".
- Consider to provide Rupture disc (RD) upstream of PSV will avoid fluid contains substances possibly precipitate / polymerize / crystallize / solidify accumulate at the inlet nozzle and pipes. (Read more in Why Rupture (RD) Upstream of Pressure Relief Valve (PRV) ?"). In the event RD is provided upstream of PSV, consider to install device to identify the potential of RD. Read more recommendation in "Why Two Rupture Discs in Series ?"
- Provide vent connection between isolation valve and PSV for depressuring during maintenance.
PSV inlet line is simple, many issues still associate with design and installation in order to ensure a well designed overpressure protection system.
Thanks to JProcess who has provided some inputs to above article.
Related Posts