Display problem ? Click HERE
Recommended :
- Tips on Succession in FREE Subscription
- Subscribe FREE - Hydrocarbon Engineering
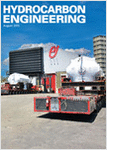
A pressure relief valve (PSV) is commonly discharge into a disposal collection system i.e flare, vent, etc. Discharge of a PSV is common smaller than the tail pipe, thus it is always swagged up to tail pipe diameter with an expander. An isolation valve is installed on the discharge of PSV so that the PSV can be isolated for testing and maintenance purpose.
A few questions raised.
i) Should the isolation valve be located between PSV and expander or downstream of expander ?
ii) The momentum (rho V2) is excessive higher than the allowable momentum criteria. Is it acceptable ?
To answer above question, first thing is to analyze the potential issue and problem associate with arrangement :
- High momentum and velocity on the tail pipe - Potentially lead to high vibration and noise level.
- Partial / Full blockage due to installation of devices i.e check valve, flame arrester, butterfly valve (read more in "Should we install Butterfly valve for Pressure Relief Valve (PSV) isolation ?"), etc - Potential lead to reduced flow, increase back pressure and causing PSV chattering. Also posses overpressure thread
- Isolation valve accidentally close by operator - potentially lead to overpressure of protected system
- Isolation valve is "self close" during blowdown due to vibration. High torque caused by asymmetric pressure distribution in the inner surface of isolation valve lead to self closure- potentially lead to overpressure of protected system
- Low pocket cause liquid accumulation - Potential severe corrosion and water hammer in the event of PSV relief
- Two phase relief - Potential of high vibration and surge
- High flow lead to severe acoustically induced vibration (AIV) may potentially lead to mechanical failure of tail pipe and valve.
- Continuous or frequent operation device i.e.manual blowdown valve, control valve discharge flow into flare system, etc may lead to high Likelihood-of-Failure (LOF)
There are a few recommendations that may be considered :
- Momentum & Velocity - Some designer may consider sonic velocity at tail pipe as discussed in "Is PSV tail pipe & lateral at CHOKED (Mach no = 1) Accpetable ?", it is always recommended to design the tail pipe below sonic velocity i.e. 70% of Mach number by increasing tail pipe line size
- Consider to install multiple PSVs i.e 2 x 50% or 3 x 33% to avoid high flow through single PSV. One shall remember, increase number of PSVs would increase number of isolation valves and probability of valve "self-close"
- Consider to install PSV with larger outlet flange to avoid high velocity of the tail pipe (before expander). Detail may refer to API Std 526
- Do not install device with potential of internal failure i.e. check valve, flame arrester, etc.
- Car Seal Open (CSO) or Locked Open (LO) of all manual isolation valve, unless required by safety analysis i.e HAZOP
- Remove handle to minimize the opportunity of operation of isolation valve and reduce potential of self closure of valve, unless required by safety analysis i.e. HAZOP
- If ball valve is installed, Full Bore (FB) ball valve to be used.
- When valve is locked by a locking plate, consider to install heavy duty locking plate to minimize potential of self-closure
- Consider to install valve with "high torque for closure" to minimize potential of self-closure
- Ensure valve (ball type) handle if facing upward to minimize potential of self-closure
- Consider to use gate valve to minimize potential of self-closure, if it is inline with plant wide isolation philosophy
- If gate valve is used, ensure the valve stem and handle is at least 45deg incline downward to avoid blockage due failure of valve internal
- Relocate isolation valve away from PSV i.e. relocated valve to downstream of reducer may reduce the risk of self closure due high vibration but it significantly increases the installation cost. Detail discussion and agreement may take place for a general approach.
- Ensure tail pipe is self drained to collection header. No pocket shall be allowed. Liquid accumulation in low pocket would result serious water hammer in the header in the event of PSV relief.
- If two phase gas-liquid is expected during relieve, ensure the tail pipe is designed for two phase relief i.e. avoid slug flow regime, enhance support, strengthen support, minimize bends, etc
- Acoustically Induced Vibration (AIV) study to be conducted to ensure the tail pipe, subheader and header is mechanically resist the severe AIV.
- If continuous or frequent operation device i.e.manual blowdown valve, control valve discharge flow into flare system, etc are installed on the system which posses high risk on Likelihood-of-Failure (LOF), may consider to conduct Flow-Induced Vibration (FIV) to ensure the tail pipe, subheader and header is mechanically resist the continuous FIV
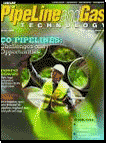
i) Should the isolation valve be located between PSV and expander or downstream of expander ?
As discussed above, relocate isolation valve away from PSV i.e. relocated valve to downstream of reducer may reduce the risk of self closure due high vibration but it significantly increases the installation cost. There are still many installation with valve just downstream of PSV has not results the self closure of valves. Thus, installation of isolation valve just downstream of PSV may be acceptable. Detail discussion and agreement may take place for a general approach.
ii) The momentum (rho V2) is excessive higher than the allowable momentum criteria. Is it acceptable ?
This is something that can not be avoided. Several check points shall be implemented.
- Ensure the tail pipe (small section) is not expose to sonic flow risk. Sonic flow would limit flow passage and reduce relief load and potentially lead to overpressure of protected system
- Minimize the tail pipe before expander i.e. fitting-to-fitting installation
- Consider series of recommendation as discussed above
Concluding Remark
Although the installation of downstream of PSV is rather simple, there are still many issue related to proper checks and installation to ensure a well design overpressure protection system.
Above is discussion on PSV discharge to closed collection system, what about discharge to ATM ? Read more in "Concerns & Measures on PSV Discharge to ATM" and "More Concerns Associated to PSV Discharge to ATM".
Related Posts
- More Concerns Associated to PSV Discharge to ATM
- Concerns & Measures on PSV Discharge to ATM
- PSV Chaterring is Destructive...The ways to Prevent...
- Concerns & Recommendations on PSV INLET line
- Is PSV tail pipe & lateral at CHOKED (Mach no = 1) Accpetable ?Should we install Butterfly valve for Pressure Relief Valve (PSV) isolation ?
- Back Pressure Affect Conventional PSV Set Pressure : Case Study #2 - Non-Bonnect Vent
- Back Pressure Affect Conventional PSV Set Pressure : Case Study #1 - Bonnect Vent to ATM
- How Back Pressure Affect Conventional PSV Set Pressure Subject to It Vent
- Several Impacts of Backpressure on Conventional PRV
- Use of conventional type PSV with back pressure exceeded 10% set pressure
- Relate PSV Relieving Flow to Stamped Capacity
- Thermal Relief of Non-Flashing Liquid in Pipe
- Simple Flow Chart to Determine Requirement of Thermal Relief
No comments:
Post a Comment